- TOP
- Enriching+TOP
- Aircraft, Bullet Trains and Rockets: Sumitomo Precision’s No.1 Products Powering Society
2025.3.17
Business
Aircraft, Bullet Trains and Rockets: Sumitomo Precision’s No.1 Products Powering Society
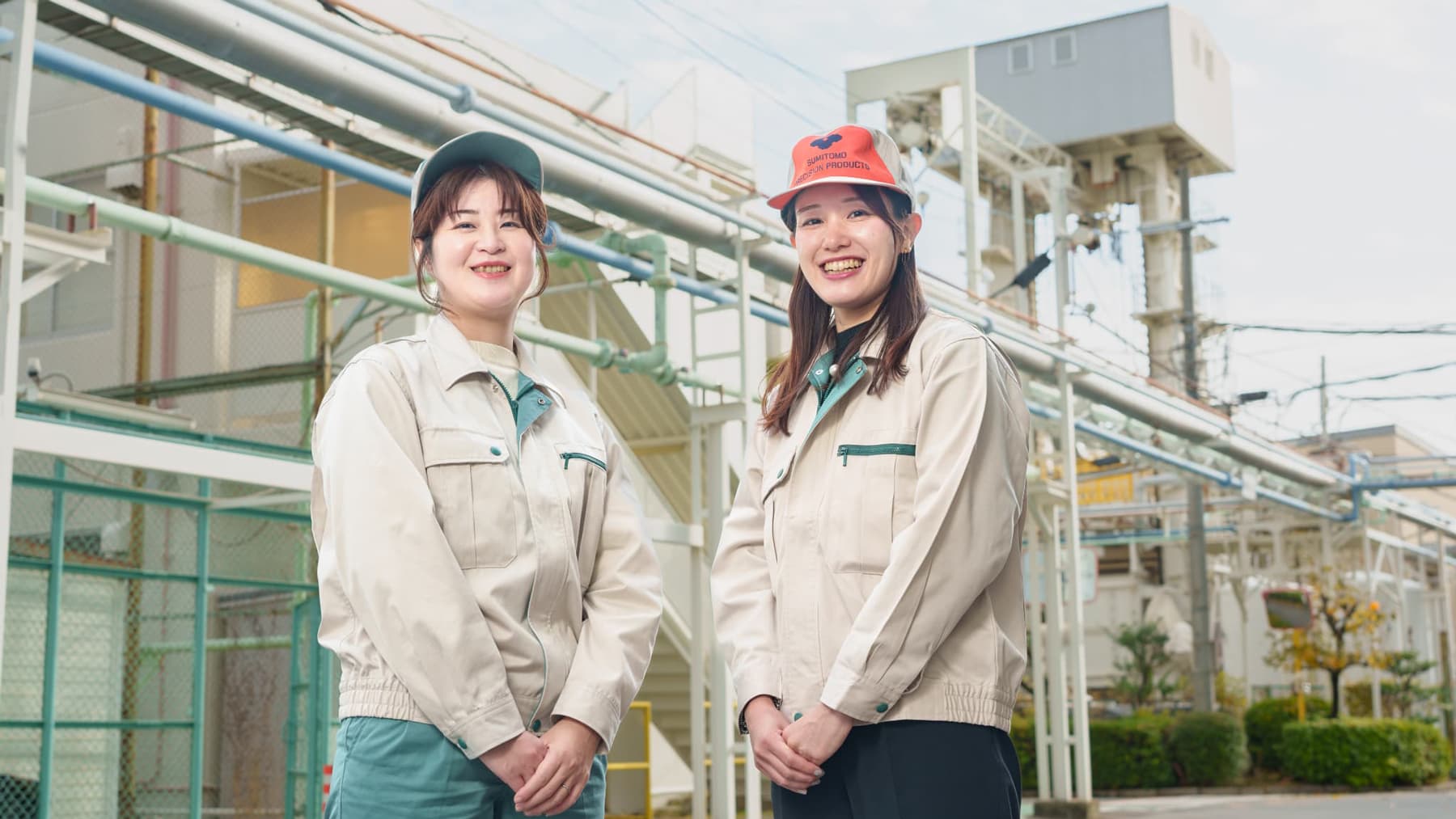
Since its establishment in 1961, Sumitomo Precision Products (SPP) has supported daily life with its unique manufacturing technologies, starting with aircraft propellers. In March 2023, it became a wholly owned subsidiary of Sumitomo Corporation, and through collaborative efforts leveraging the strengths of both companies, is working to expand its business. In this interview, Seiko Sugahara, Public Relations at SPP, introduces three of the company's key products that are not only essential to everyday infrastructure, but also at the frontier of space exploration. Haruka Masuda, who is responsible for promoting business with SPP at Sumitomo Corporation, will interview her.
-
General Affairs Group, General Affairs and Human Resources Department, Sumitomo Precision Products
Seiko Sugahara
After working in local government and at a food manufacturer, Sugahara joined SPP as a mid-career hire. In the General Affairs Group, she handles a wide range of PR duties. Her personal motto is "Doing work that benefits society."
-
Aerospace Defense & Technology SBU, Sumitomo Corporation
Haruka Masuda
Masuda joined Sumitomo Corporation as a new graduate and was assigned to the Planning & Coordination Dept., Transportation & Construction Systems Business Unit, where she was responsible for human resources and performance management. In her current role, she oversees operations related to SPP.
- From Aircraft Propellers to Small Rocket Sensors: Powering Society for Over 60 Years
- The Only Aircraft Landing Gear Manufacturer in Japan: Connecting SPP's Core Business to the Next Generation
- Heat Exchangers in Every Bullet Train Since Inception, Now Applied to Data Centers
- Joint Development with JAXA: High-Precision Gyroscopes for Domestic Rockets
- Leveraging SPP's Technical Expertise With Sumitomo Corporation's Network for Further Growth
From Aircraft Propellers to Small Rocket Sensors: Powering Society for Over 60 Years
MasudaSPP started with the manufacturing of aircraft propeller and today also handles small sensors for rockets. Could you tell us about the company's journey?
SugaharaSPP was established in 1961, inheriting the aircraft equipment business unit of Sumitomo Metal Industries (now Nippon Steel Corporation). We started with the manufacturing of propeller and gradually expanded the business into aircraft landing gear, heat exchangers for engine and other technology.
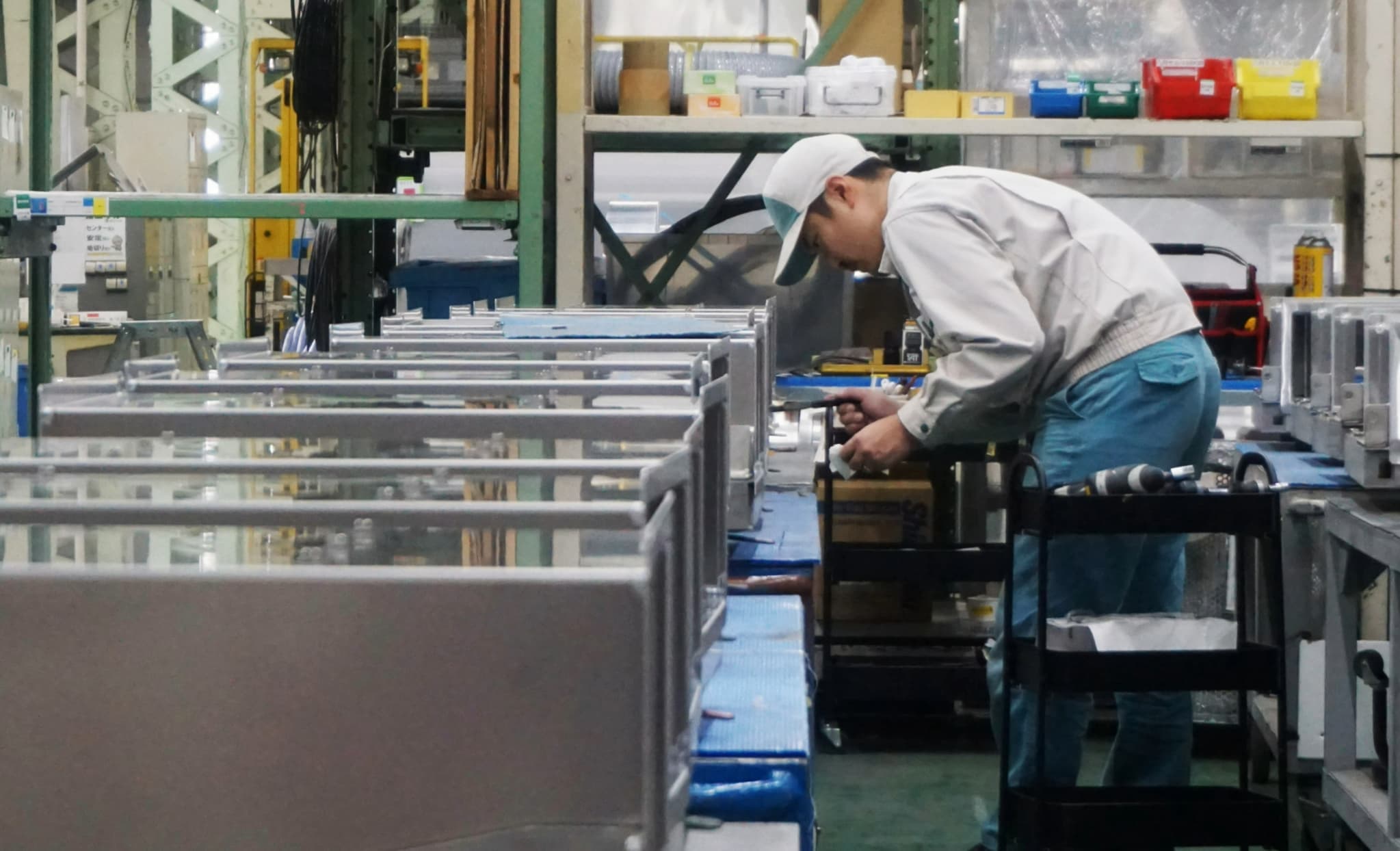
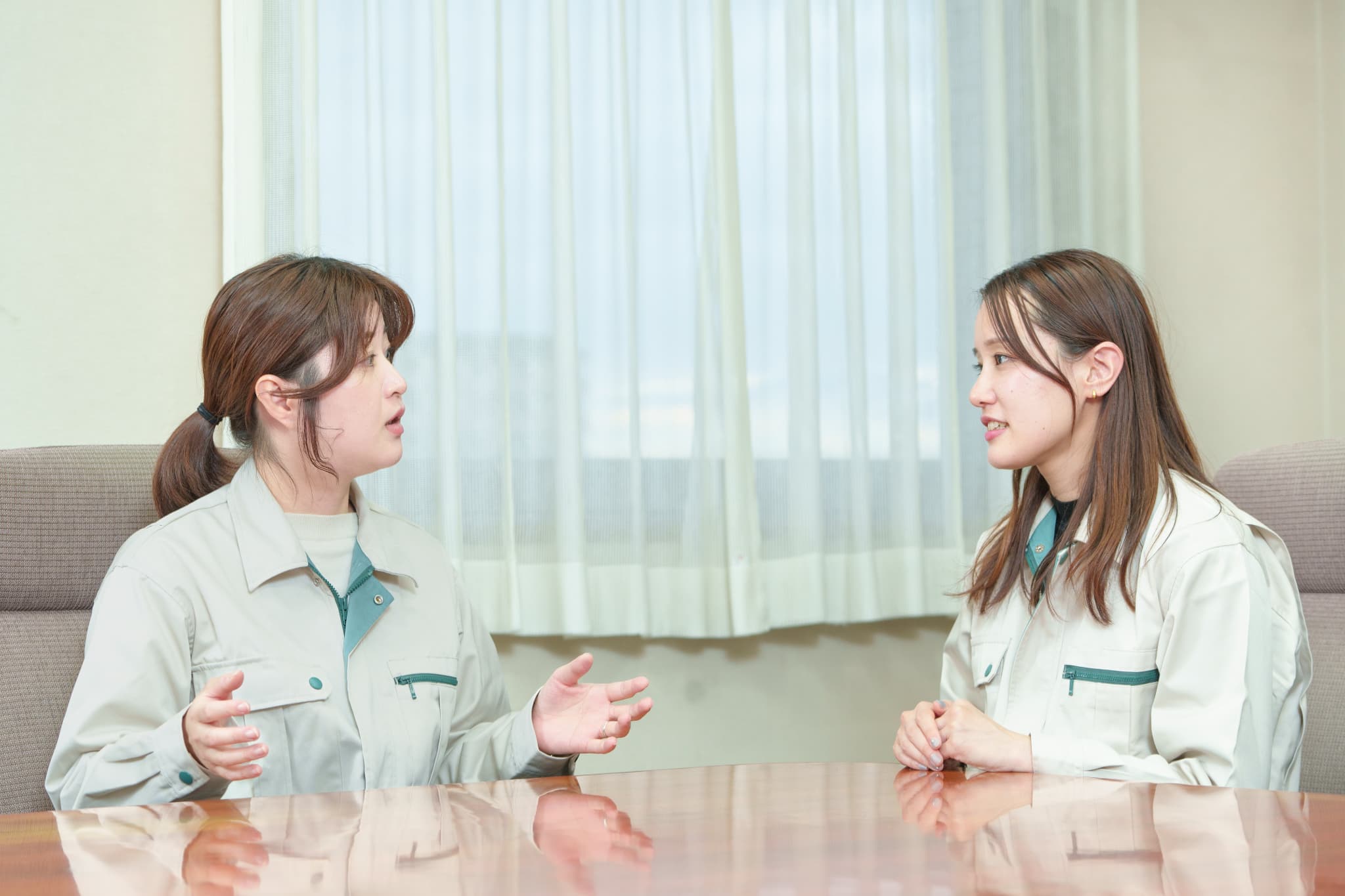
MasudaIncidentally, it was Shunnosuke Furuta, the last director-general of Sumitomo Head Office, who initiated SPP’s involvement in aircraft propeller. Furuta was also a major figure in the establishment of Sumitomo Corporation. Both companies inherit the spirit of Sumitomo’s business philosophy. It's quite a moving tale that SPP became a wholly owned subsidiary of Sumitomo Corporation in 2023.
Later, SPP applied its aircraft technology to venture into the industrial machinery sector, correct?
SugaharaThat's correct. We supply a diverse range of heat exchangers, including rolling stock such as bullet trains, alongside power equipment and other sectors of industry and society. We also manufacture hydraulic control pumps used in injection molding machines for producing plastic products and more.
In addition, we have established an ICT (Information and Communication Technology) business as part of new business development initiatives. In this area, we provide products such as "ozone generators" used in semiconductor manufacturing, MEMS(*1) devices, and MEMS/semiconductor manufacturing equipment essential for realizing a smart society. Across these diverse businesses, we have many products that hold top market share in Japan.
(*1) Micro Electro-Mechanical Systems, widely used in smartphones and automobiles with automatic control functions.
The Only Aircraft Landing Gear Manufacturer in Japan: Connecting SPP's Core Business to the Next Generation
SugaharaFurther examples include the manufacture of aircraft landing gear. We are the only landing gear manufacturer in Japan, handling both commercial aircraft like the Bombardier (now MHIRJ) "CRJ" and military aircraft for the Ministry of Defense. Globally, there are only a handful of manufacturers that can independently design, manufacture and test landing gear for small jet airliners.

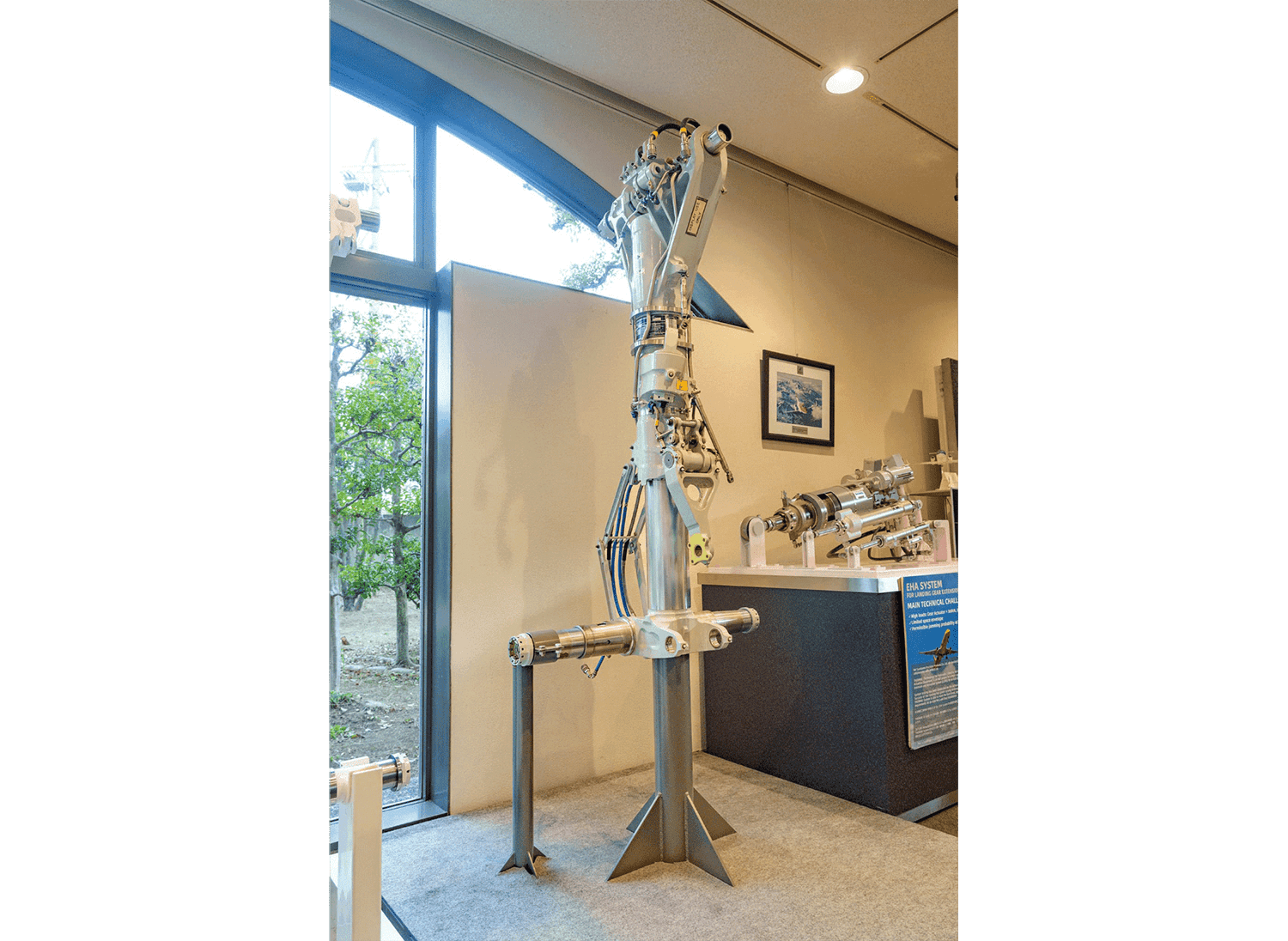
MasudaHow have you developed such unique technologies?
SugaharaIn the years since our founding, we have built a strong foundation of technical excellence through expertise and equipment development in aircraft technology. For example, the material for the landing gear is a steel called "300M," which is three to five times harder than the steel used in general industries. We have advanced technology to process such hard steel to micron-level precision. Additionally, owning specialized test facilities, such as landing gear drop test towers, is another major strength.
International safety standards for aircraft parts continue to rise every year, and they include a wide range of requirements, including how to respond when parts other than landing gear fail. SPP leverages the knowledge gained from past development to propose designs that minimize risks. I think it would be very difficult for other companies to abruptly enter this field and match our level of expertise.
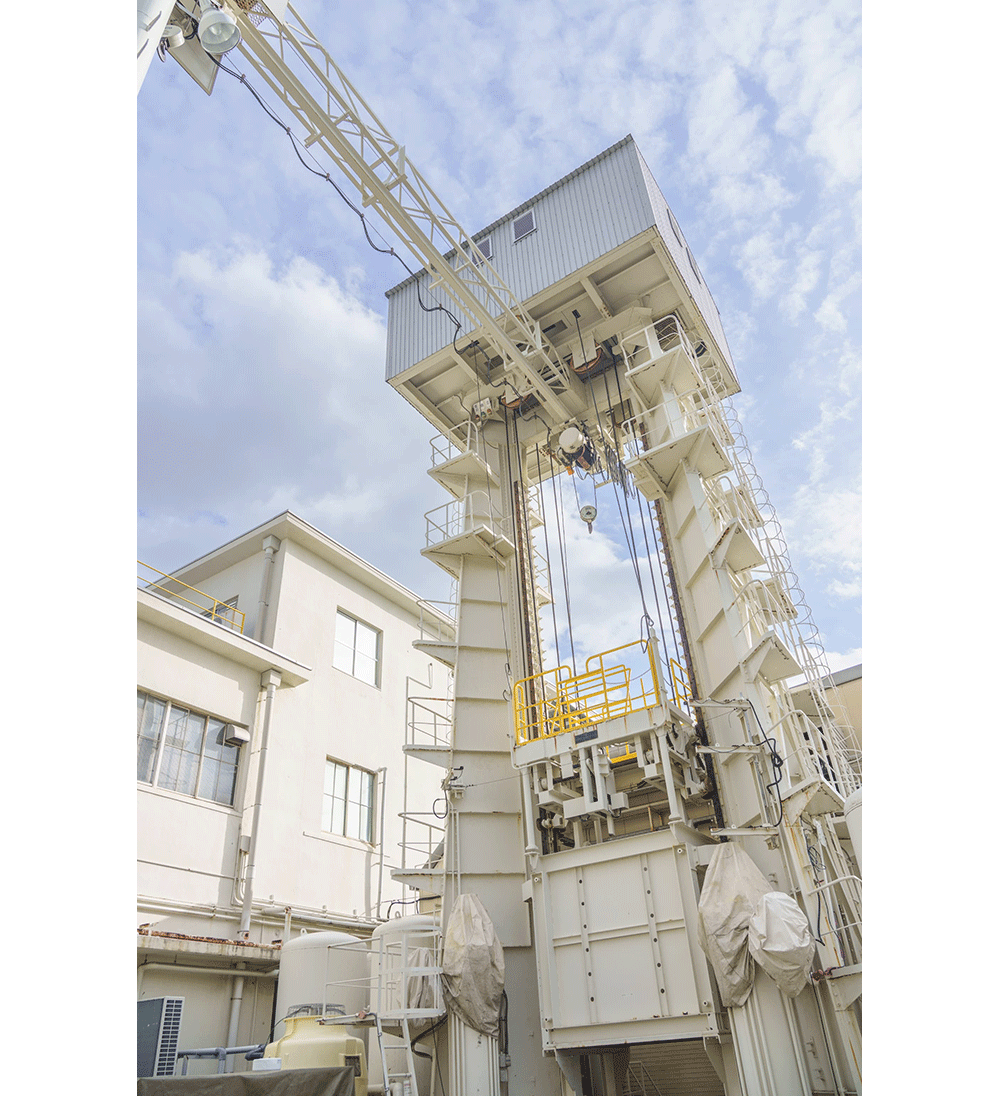

MasudaWhat kind of team structure is in place for landing gear development?
SugaharaTo ensure the transfer of technical knowledge, we have a balanced team of 20 to 30 members, including veterans, junior staff and mid-career professionals. Aircraft development opportunities come up about once every ten years. When those opportunities arise, we actively involve the next generation of engineers. We are also working on developing landing gear for electric aircraft. Landing gear is the cornerstone of SPP's business, and our products are used in aircraft dispatched for disaster relief in Japan and humanitarian missions overseas. Our team takes great pride in that.
Heat Exchangers in Every Bullet Train Since Inception, Now Applied to Data Centers
SugaharaNext, I'd like to talk about heat exchangers for bullet trains. These heat exchangers are used to cool the heat generated during train operation, and several types are installed in each car. SPP heat exchangers have been used in all bullet train models, from the original 0 Series that launched in 1964 to the latest N700S. Specifically, the heat exchangers for the main transformers(*2) which is one of the important components of the bullet train, and the heat exchangers for the brakes are 100% SPP-made. While they are just one component, we take great pride in creating something irreplaceable and indispensable.
(*2) A device that converts high-voltage electricity from the overhead wire to a voltage suitable for controlling the bullet train.
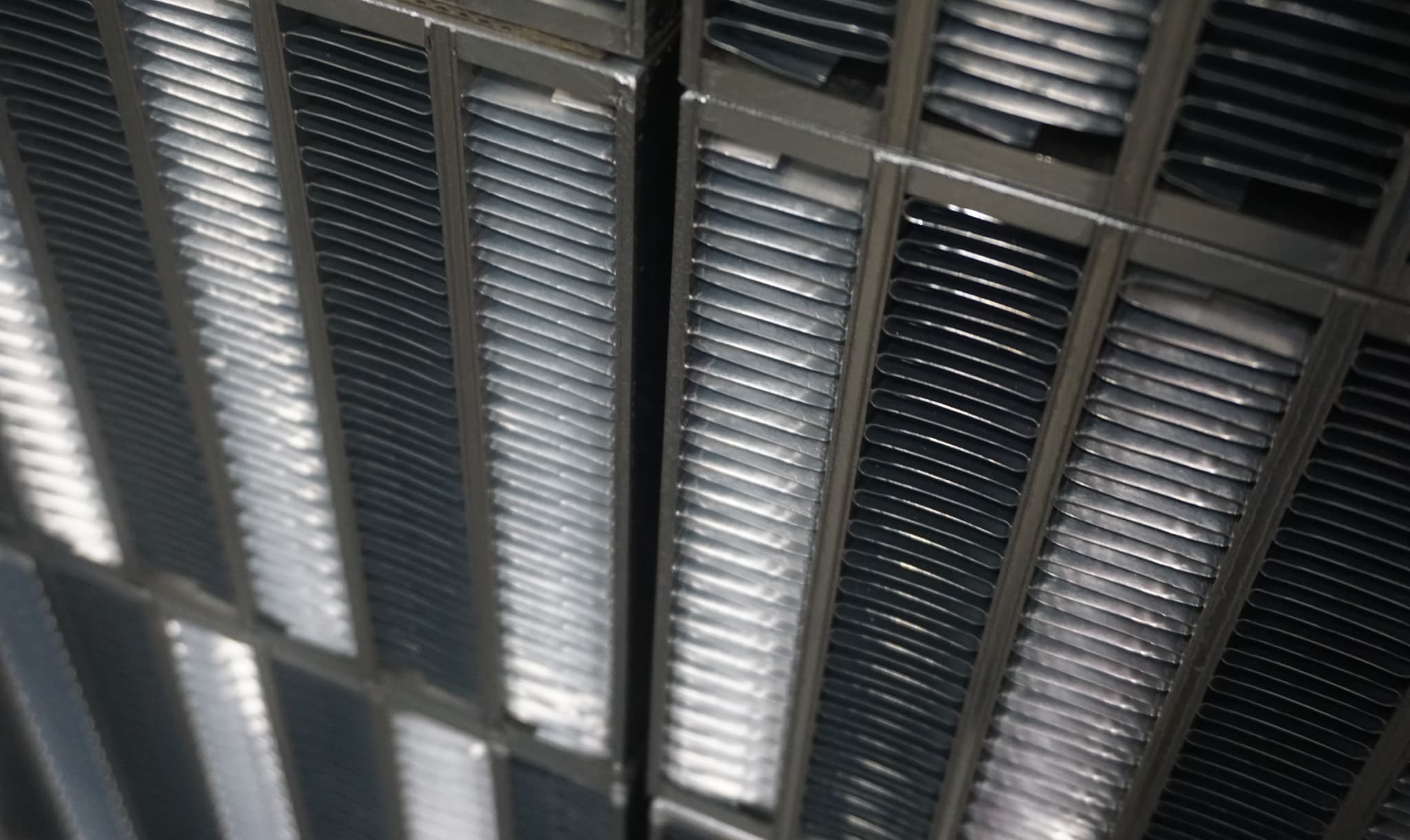
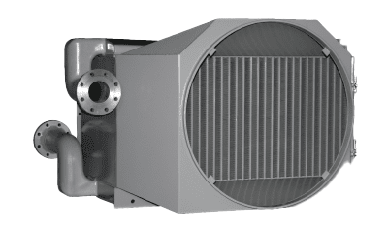
MasudaSo it's safe to say that SPP's 50-plus years of experience in heat exchangers gives you expertise and technology that other companies simply can't replicate?
SugaharaPrecisely. The heat exchangers used in bullet trains are quite large compared to those used in cars, measuring about one meter long. The aluminum alloy used in the heat exchangers is inherently difficult to weld. The technology we use to reduce the number of welding processes and assemble them by hand, then join them using "vacuum brazing" is a true form of craftsmanship. We pride ourselves on world-class technology, and not only are we involved in overseas railway projects like the Taiwan High Speed Rail and the UK's High-Speed Rail, but we also handle different types of heat exchangers in the energy sector, including LNG (liquefied natural gas) vaporization units.
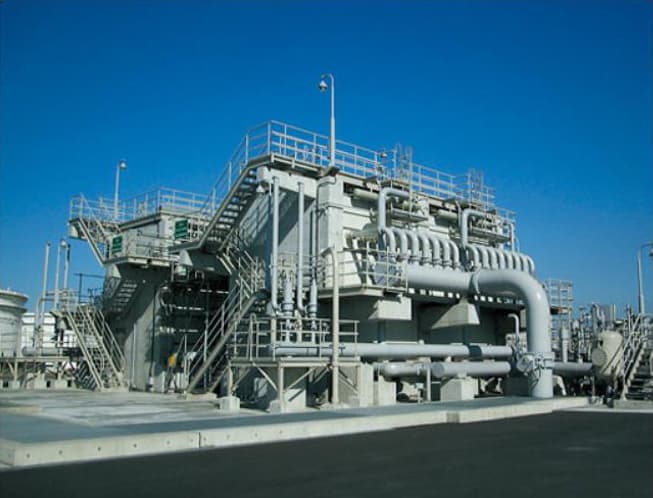
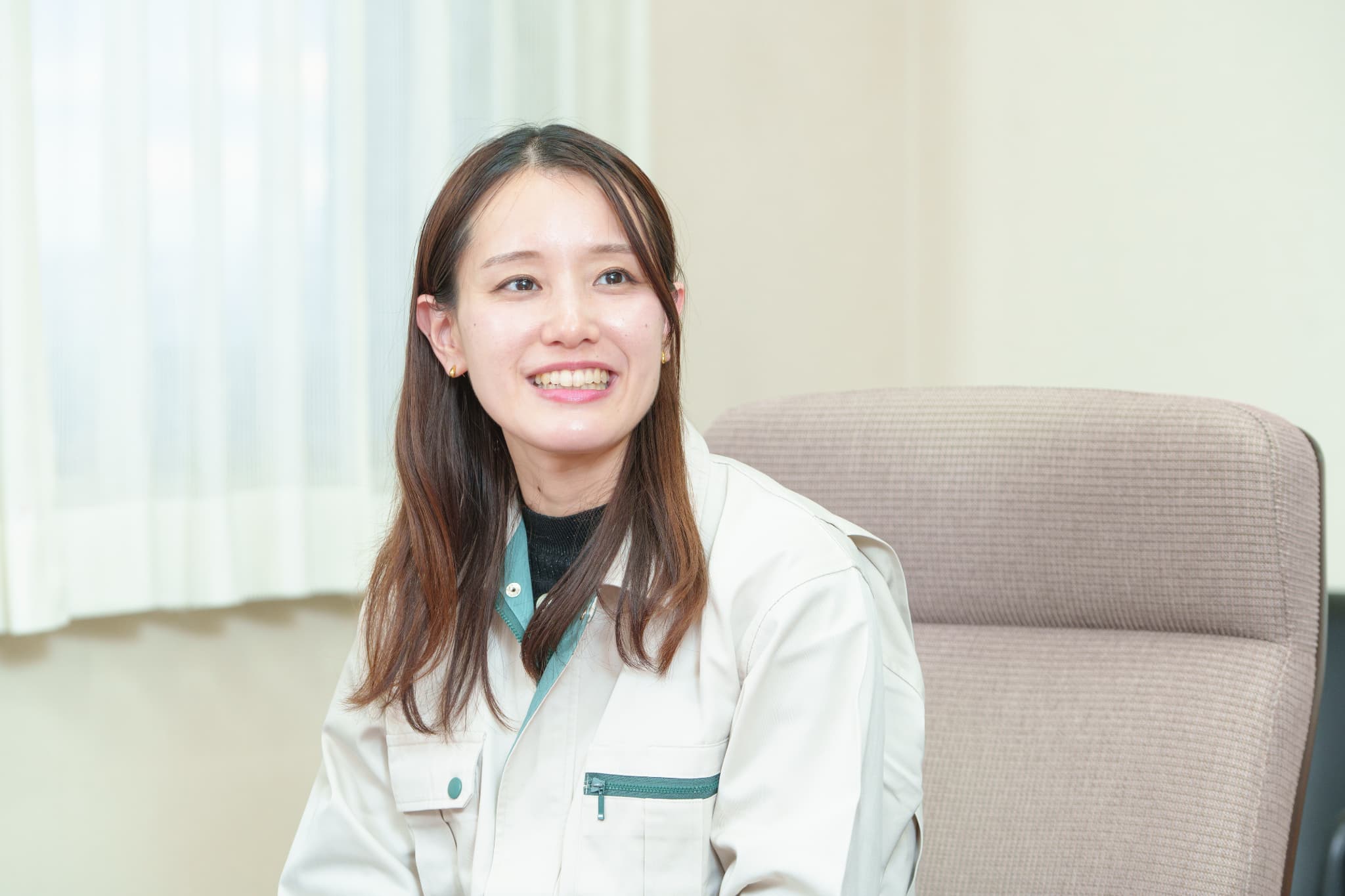
MasudaRecently, I believe SPP is applying its bullet train technology to manufacture heat exchangers for data centers as well, right?
SugaharaYes. With the increasing number of data centers being established to house high-performance servers in our information-driven society, we are working to create new business opportunities. Heat exchangers for data centers are small – about 10 cm squared – but they generate a large amount of heat per unit area, requiring high-performance cooling solutions. That's why we're applying the specialized heat exchange technology used in bullet trains to create prototypes.
When developing products for data centers, it's important to catch the needs of large international tech companies, who will be the end users. We hope to strengthen our collaboration with Sumitomo Corporation, which has a global business network, to expand our reach in this sector.
Joint Development with JAXA: High-Precision Gyroscopes for Domestic Rockets
SugaharaFinally, I'd like to talk about the high-precision gyroscope used for flight trajectory monitoring system on the Japanese flagship rockets. This system monitors whether the rocket is deviating from its planned trajectory. Essentially, it serves as a safety mechanism for the rocket. SPP is the only company in Japan manufacturing the gyroscope used for this system. The MRN-01, which SPP developed in collaboration with JAXA, is scheduled to be installed in rocket like the H3.
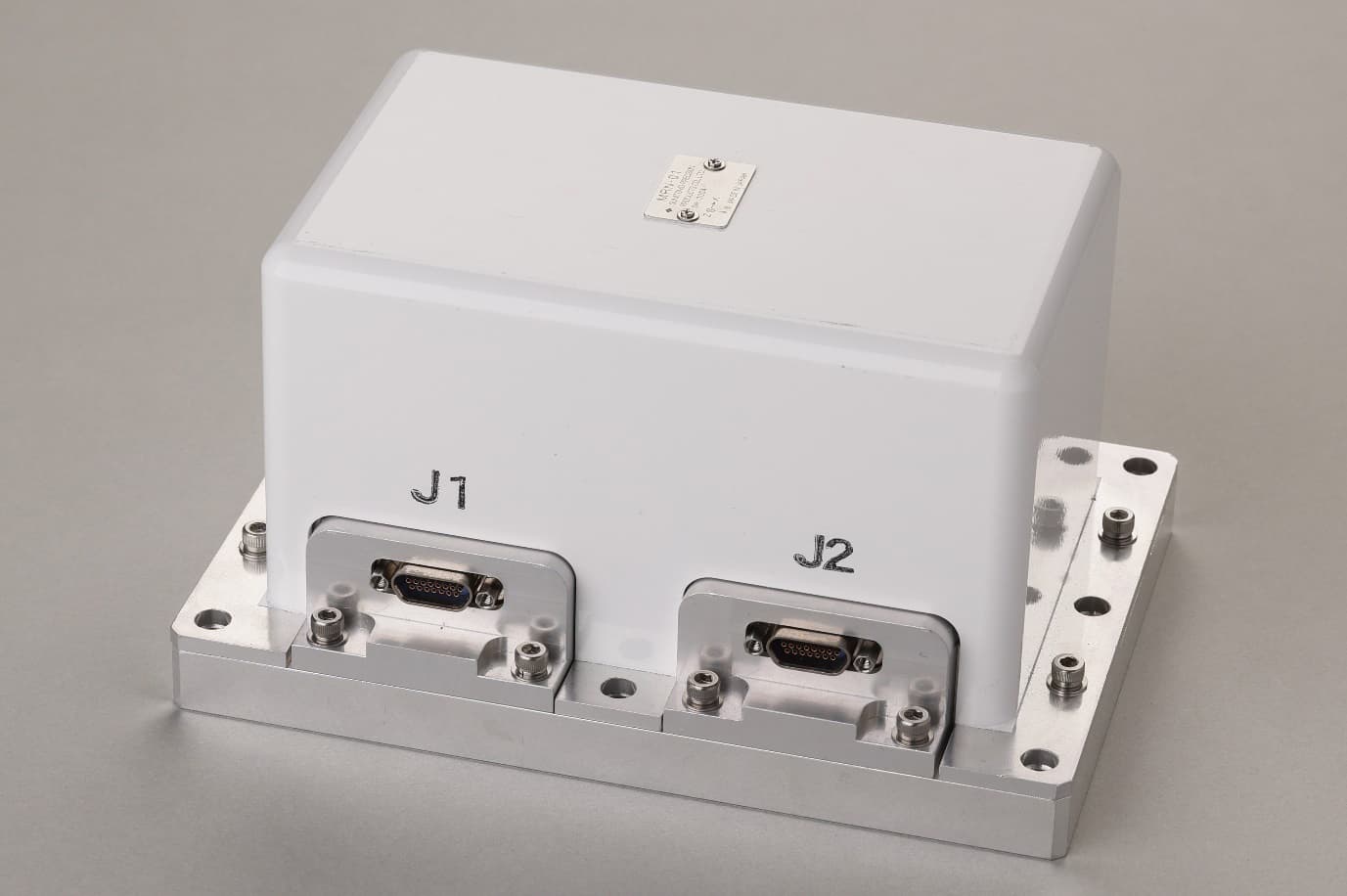
MasudaWhat led to joint development with JAXA?
SugaharaOriginally, SPP had been manufacturing sensors that detect angular velocity using MEMS technology (MEMS gyro). These sensors are installed in everyday devices like smartphones and gaming consoles, and common models are relatively inexpensive, costing less than 1 USD each. However, SPP wanted to differentiate itself by focusing on ultra-high precision. MEMS manufacturing requires advanced technology to process materials in 3D at the micron level, thinner than human hair. One applicable strength in this regard is our in-house manufacture of the silicon etching equipment essential for MEMS production.
The turning point came in 2012 when we participated in an open joint research program sponsored by JAXA, where SPP's advanced processing technology and the potential of our MEMS gyros were recognized. Afterward, JAXA decided to initiate a project to develop a domestic product that was both more affordable and offered higher performance than existing foreign-made alternatives. The convergence of this requirement specified by JAXA and SPP's technical capabilities led to the creation of the "MRN-01."
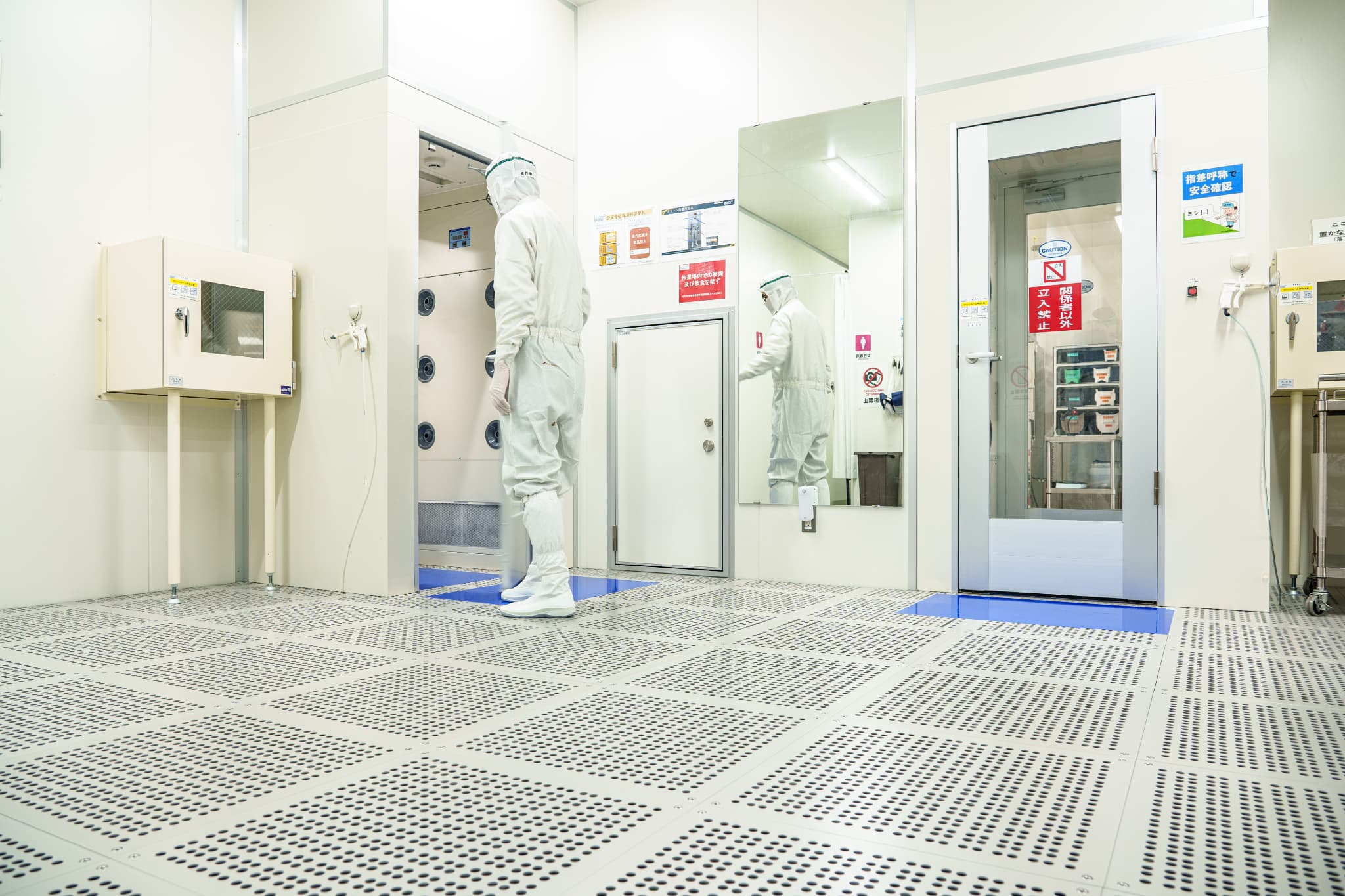
MasudaWere there any challenges in developing the product for use in space?
SugaharaYes, working in space comes with many strict requirements, such as reliability and environmental resistance, so we faced many challenges in testing and analysis. For example, resistance to radiation, vibration and shock during launch. Also, once something is in space, it cannot be retrieved if it breaks, so we ensured redundancy by installing two sensors for one sensing axis. After a lot of trial and error, we successfully conducted a space demonstration in 2021.
MasudaLeveraging your space development experience, you are also developing equipment used in mining for resource extraction, right?
SugaharaYes, we are developing a product called "Northfinder." Just like space, the environment inside the Earth – such as in mines – is harsh, so our space expertise is definitely applicable.
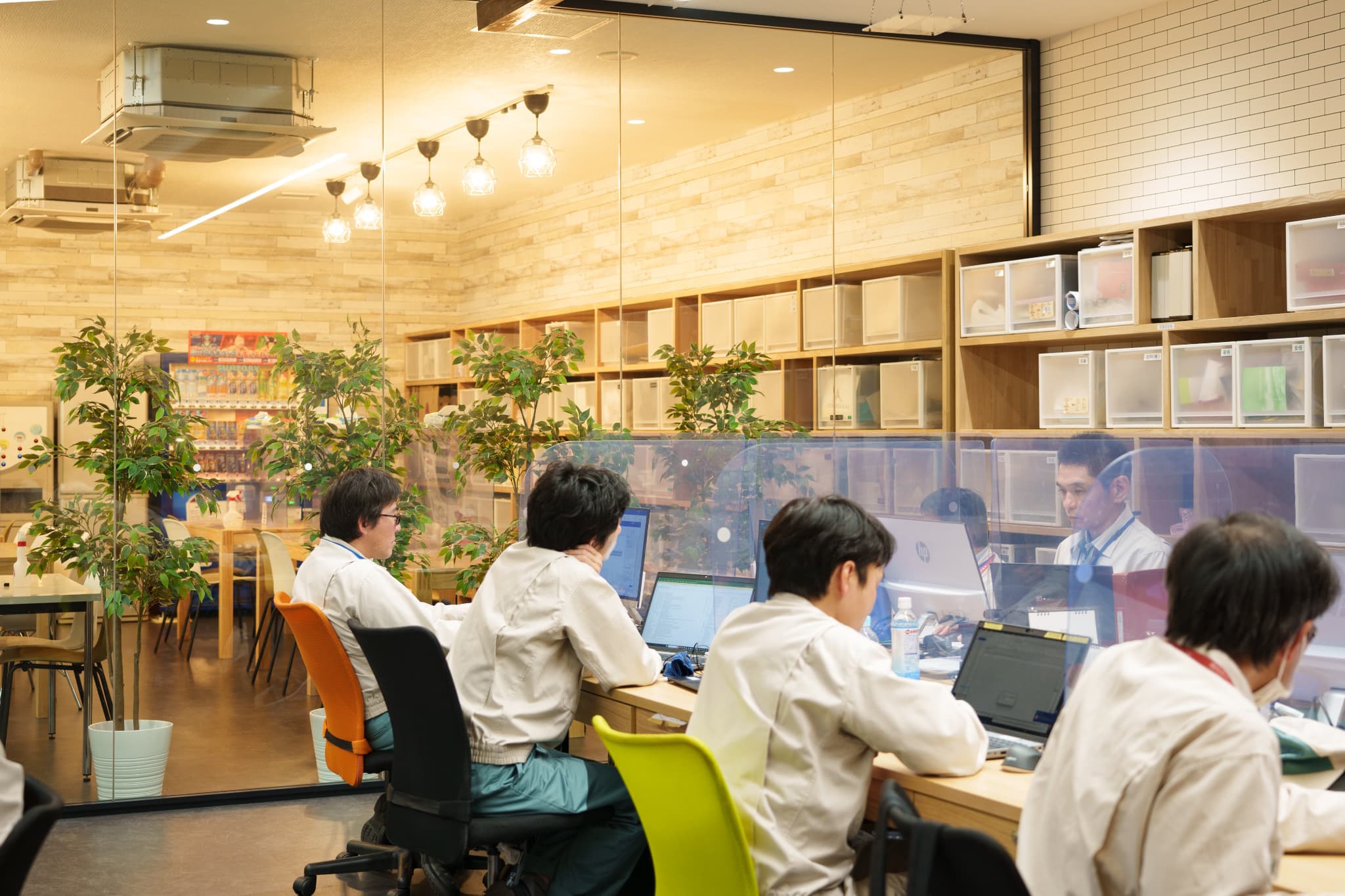
Three "No.1 Products" of SPP
- Aircraft Landing Gear: 100% domestic market share. SPP is one of the few manufacturers worldwide that can design, manufacture and test landing gear for small jet airliners in-house.
- Bullet Train Heat Exchangers: Installed in all bullet train models, from the original 0 Series to the latest N700S. The heat exchangers for the main transformer and brakes are 100% SPP-made.
- High-Precision Gyroscopes for Domestic Rockets: SPP is the only company in Japan manufacturing this product. SPP has also ventured into space through joint research with JAXA.
Leveraging SPP's Technical Expertise With Sumitomo Corporation's Network for Further Growth
MasudaOnce again, I've realized the depth of SPP's technological and developmental capabilities, accumulated over more than half a century. With new products being developed across diverse businesses to align with the changing times, SPP is expanding new technologies into even broader fields, and Sumitomo Corporation is leveraging its network to help make this possible. SPP has set targets of 100 billion yen in sales, 10 billion yen in operating profits and a 10% profit margin by FY2030, and at Sumitomo Corporation we are committed to helping achieve these goals, however possible.
SugaharaWhile SPP has strong technological capabilities, we are hoping to improve how we share information and forge relationships with new customers. In that sense, Sumitomo Corporation's broad vision, wide network and multilingual capabilities are invaluable. By combining our strengths, I believe we will create even better business opportunities. Not only will we continue to support infrastructure essential to society, but we also aspire to drive technological innovation that excites people about the future.
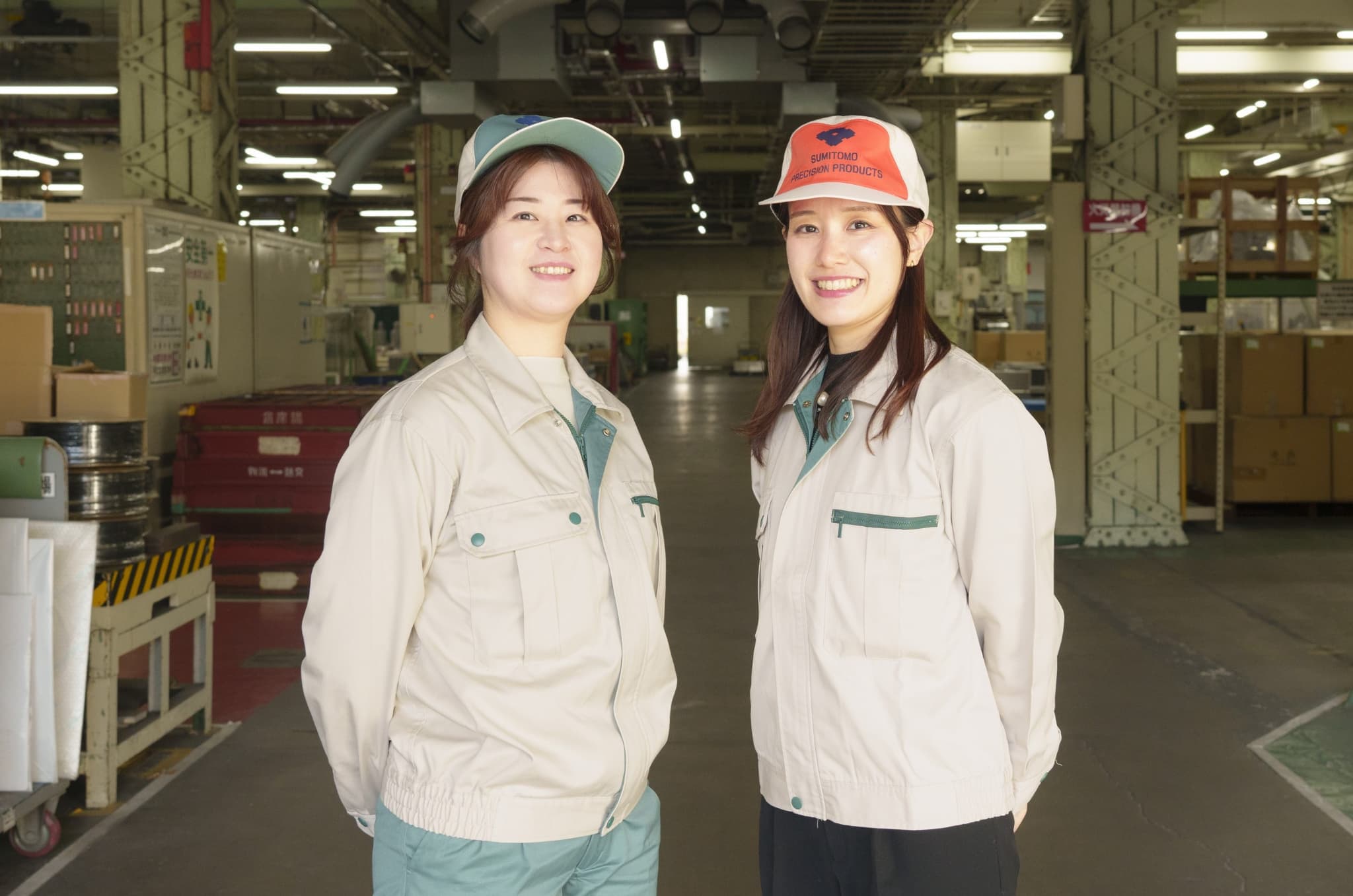